In recent years, more and more enterprises have embraced autonomous vehicles as a cornerstone of their operational strategy. Autonomous reversing technologies are one of the most important components in this process- allowing cars to identify obstacles, take appropriate measures to avoid them, and back up with precision.
From engineering challenges to ethical dilemmas – there are many issues surrounding autonomous driving and reversing that must be addressed before it can be implemented on a wide scale basis. In this case study we’ll explain the solution we’ve implemented to solve this particular issue of trucks reversing into tight loading bays in distribution centres and logistics sites and the results site managers can expect, by adopting these promising new advancements in automation technology and getting ahead of their competitors.
Background – Why is autonomous reversing a challenge?
As part of the 5G CAL project at Nissan Sunderland established to automate the industrial logistics beyond ‘the confines of the factory’, StreetDrone set themselves the challenging task of developing self-driving technology to take charge of heavy goods vehicles delivering supplies to various parts of a large and complex manufacturing site.
With a full-stack capability to develop driving robots and software with associated AI systems to provide autonomous driving, StreetDrone did have to address one use case that had not previously arisen in previous operational design domains. How to reliably, safely and accurately reverse park a 40ft HGV tractor and trailer in a loading bay that provided a mere 15cm of lateral tolerances.
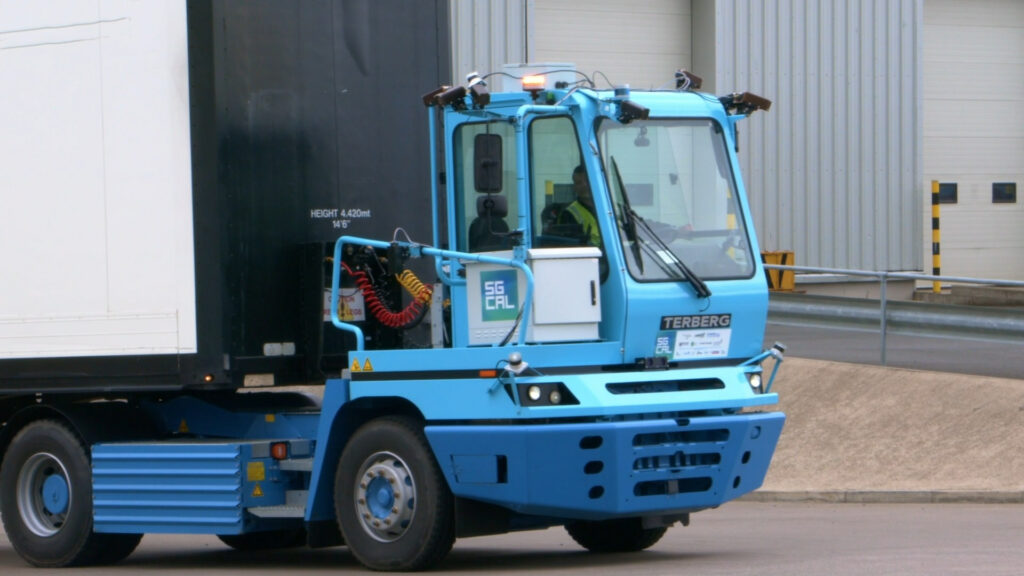
The Problem – Space-constrained autonomous reversing of a truck and trailer system
The task set by the 5G CAL project was to move goods in HGV trailers with an autonomous electric yard shunter from a distribution centre on the perimeter of the Nissan Sunderland manufacturing site. The route requires a stop and validation process at a barriered checkpoint, after which the vehicle follows an arterial roadway used by other vehicles to the delivery point.
However, the final part of the route provided the most stringent challenge. The delivery location is a typical goods-in warehouse with HGV loading bays, which demanded the automated technology to provide a complex reverse park manoeuvre.
This requirement sits outside of scope of existing autonomous driving algorithms, requiring StreetDrone to develop a ground up solution.
The path planning and motion control of reverse parking an articulated vehicle are mathematically complex and in manual operation, represents one of the most highly skilled aspects of specialist driving.
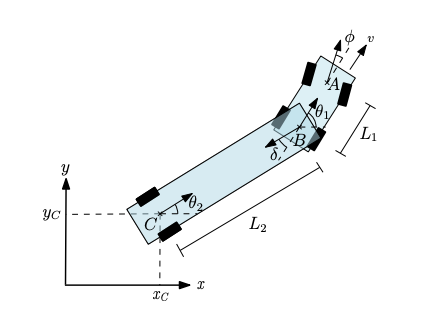
However, consistent with StreetDrone’s broader engineering philosophy, automation solutions must be quickly deployable and where possible, use retrofit to avoid large capital outlays. For this reason, the project had no alternative but to automate the highly challenging physics of the tractor & trailer reverse park.
The Solution – How we demonstrated a successful, reverse-only parking in trailer bays
Consistent with the StreetDrone approach to make technology deployable in order that customers can benefit immediately from the efficiency and productivity gains, the problem was broken down into two parts.
In phase 1, engineers adopted a teleoperation solution for the final, reverse park manoeuvre. This allowed the autonomous system to operate across the majority of the journey and effectively hand control to a manual driver for the skilled reversing operation. Phase 1 required both technical development but delivered immediate efficiency gains.
The technical development required to deliver phase 1 was the creation of a cyber secure and seamless transfer of vehicle control between an autonomous state and a remote operator.
The adoption of teleoperations enables a remotely located, skilled HGV driver to manage a fleet of vehicles, thereby delivering immediate gains given the current shortage of professional drivers.
The teleoperations solution enabled the automated logistics service to move into an operational phase while the development of the elements of the fully autonomous system – the algorithm and hardware solutions – were developed.
Phase 2
The main challenge in the physics of reverse parking is the compounding problems created by steering inputs that are controlling outcomes 40ft distant. Small errors in the manoeuvre create exponentially larger deviations from the ideal path. Moreover, the correction equation becomes significantly more complex by virtue of the vehicle articulation.
For manual drivers, the solution is forward correction – ie, if the trailer varies from an ideal pathway when reversing, the driver corrects the pathway by pulling forward. For even skilled HGV drivers, reversing into a loading bay often takes at least one forward correction.
One approach to the problem is to mathematically process steering angles and distance. But this relies on the environment being true and known. Moreover, this approach demands a heavy processing capability which can be challenging for an embedded system. The net consequence of these factors ultimately results in an unstable solution.
Having ruled this approach out as unfit for purpose, StreetDrone’s engineers fixed on an adaptive approach. This plots a target path and relies on continuous assessments and adjustments of the steer angles to keep the manoeuvre on the target path. The solution relies on LiDAR scans of the environment and sensor data for the vehicle to understand its position in context.
After a series of tests and development of the self-driving stack, including sensor solutions that allow the algorithm to record the trailer articulation angles, engineers were able to demonstrate successful, reverse-only parking in trailer bays bound by lane dividers that provided only 15cm of clearance on either side of the trailer.
The Benefits – Drive efficiencies through high levels of automation
The solution developed by StreetDrone has extended industrial automation for the first time to the more complex and challenging environment ‘outside of the factory.’ It offers the capability to drive efficiencies through high levels of automation with a seamless teleoperation layer providing a safety provision.
The solution is also agnostic to the delivery bay topography and can be applied to a variety of different trailers without need for time-consuming calibration. In terms of deployability, the self-driving stack can be retrofitted to existing yard shunters and delivery yards require no modification, providing automation benefits without costly capital expenditure.